Closed-Loop Control in DC Servo Motors
Closed-Loop Control in DC Servo Motors
How Feedback Mechanisms Enhance Accuracy and Stability
In the world of precision motion control, DC servo motors are a trusted workhorse. Known for their fast response, smooth operation, and precise positioning capabilities, these motors are widely used in robotics, automation, CNC machinery, and aerospace systems. However, their effectiveness hinges not just on motor quality or mechanical design, but on the control strategy—and specifically, the use of closed-loop control systems.
Unlike open-loop systems that operate without real-time feedback, closed-loop control uses sensors and intelligent algorithms to continuously monitor and correct the motor’s position, speed, and torque. The result is a highly responsive system capable of maintaining accuracy even in the presence of disturbances, mechanical loads, or variable operating conditions.
This article explores how feedback mechanisms form the backbone of closed-loop DC servo motor control, and how they contribute to superior accuracy, stability, and dynamic performance.
1. What Is Closed-Loop Control?
Closed-loop control, often referred to as feedback control, is a system in which the output of a device is continuously measured and compared to a desired setpoint. Any deviation (error) between the actual output and the setpoint is used to generate a corrective input that adjusts the system accordingly.
In the context of DC servo motors, this means:
•Measuring the actual position, velocity, or torque using sensors.
•Comparing these values to a desired command from a controller.
•Adjusting the motor's drive signal in real time to eliminate error.
This continuous feedback and correction loop is what allows servo systems to deliver precise, repeatable motion, even under fluctuating loads or external disturbances.
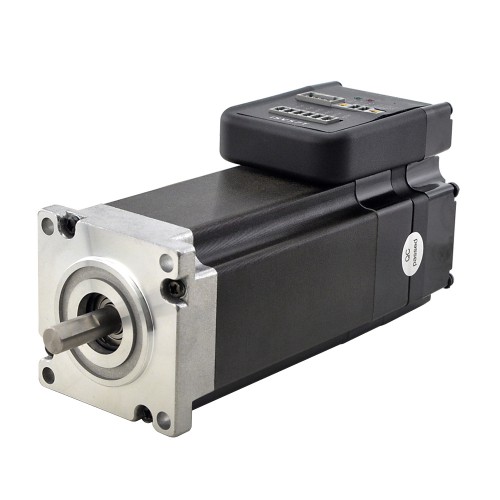
Picture from: iSV57T-180S
2. Key Components of a Closed-Loop DC Servo System
A typical closed-loop servo motor system includes several essential components:
a. The Motor
Usually a brushed or brushless DC motor, selected for its speed and torque characteristics.
b. Feedback Device (Sensor)
Encoders or resolvers are commonly used to provide real-time information about the rotor’s position and speed. Some advanced systems also include torque sensors or current feedback for more complex control.
c. Servo Controller (or Drive)
The brain of the system, it interprets sensor data, runs control algorithms (such as PID), and adjusts the motor’s voltage or current to match the commanded input.
d. Power Electronics
These amplify the control signals and deliver the necessary current and voltage to the motor windings.
Together, these components form a tight control loop that enables high-precision performance.
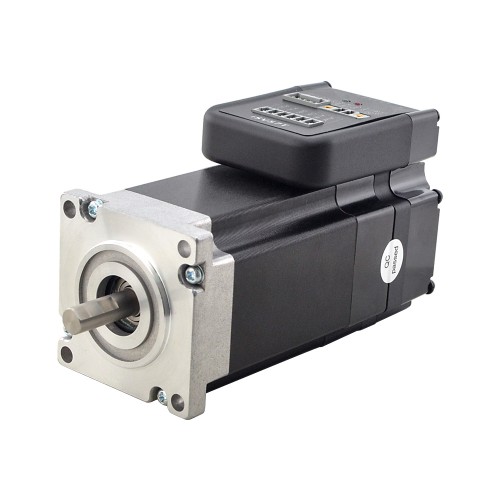
Picture from: iSV57T-130S
3. The Role of Feedback in Enhancing Accuracy
One of the primary advantages of closed-loop control is positional accuracy. In open-loop systems, the controller assumes the motor moves exactly as commanded. But in real-world conditions, this assumption often fails due to friction, load variation, or mechanical backlash.
In contrast, closed-loop systems use feedback to detect even tiny errors in position or speed. For example, if the system is commanded to move the motor shaft to 90 degrees, but it only reaches 88 due to load torque, the controller will detect the error and adjust the drive signal to reach the correct position.
This continuous correction enables:
•Precision at microstep levels, crucial in applications like pick-and-place machines and optical systems.
•Load compensation, allowing consistent performance under varying mechanical demands.
•Zero position drift, which is especially important in long-term or repetitive operations.
4. Enhancing Stability Through Control Algorithms
Closed-loop systems are not just accurate—they are also inherently more stable than their open-loop counterparts. This stability is achieved through control algorithms that intelligently adjust motor behavior based on feedback.
The most common algorithm is the PID controller, which consists of:
•Proportional (P): Corrects present errors.
•Integral (I): Addresses accumulated past errors.
•Derivative (D): Anticipates future errors based on rate of change.
When tuned properly, a PID controller ensures that the motor responds quickly and smoothly without overshooting or oscillating. For more demanding applications, modern controllers may use model predictive control (MPC), adaptive control, or artificial intelligence to enhance dynamic performance.
5. Real-World Benefits of Closed-Loop Servo Control
The implementation of feedback-based control systems in DC servo motors yields several tangible benefits across a wide range of industries:
a. Improved Responsiveness
Servo systems can quickly adapt to changes in command or external forces, making them ideal for dynamic environments such as robotics or automotive testing platforms.
b. Higher Energy Efficiency
Because the system continually adjusts current and voltage to match load requirements, power usage is optimized—reducing energy waste and thermal stress.
c. Fault Detection and Safety
Closed-loop systems can detect anomalies such as stalls, overspeed conditions, or sensor failures in real time, enabling fast shutdowns or alerts that prevent damage.
d. Precision Synchronization
In multi-axis systems, feedback enables perfect coordination between multiple motors, which is critical in automation, 3D printing, and synchronized conveyor systems.
6. Challenges and Design Considerations
While closed-loop control offers superior performance, it also introduces complexity:
•Sensor Integration: Adding encoders or resolvers increases system cost and design effort.
•Tuning Requirements: PID parameters must be carefully adjusted for stability across all operating conditions.
•Signal Noise and Latency: High-resolution feedback can be sensitive to electrical interference or delays, requiring filtering and robust communication protocols.
•System Bandwidth: The controller’s processing speed and loop rate must be sufficient to respond effectively to rapid changes.
These challenges must be considered during the design phase to fully leverage the advantages of closed-loop control.